Inorganic fibers
General remarks
Inorganic fibers, both metal and non metal ones, are more resistant, more rigid, have an higher melting point and are more heat resistant than traditional fibers.
They are also totally uninflammable, but, except for the metal ones, they are fragile. Their textile importance is also limited, whereas they are widely used as reinforcement in composite materials.
They are usually excellent in high temperatures and in a corrosive surrounding.
Real fibers with an area transversal section lower than 0,005 mm2 and a thickness lower than 0,25 mm are carried out. We can get them as wiskers (= mono crystalline materials) and as real fibers, both continuous and cut in cluster.
Their diameter changes from 5 to 15 nm, but other ones are much thicker, like the ones got through vapor deposition on the fibers, such as borate fibers and silicon carbide fibers (100-150 n).
The diameter of the fiber is critical compared to its resistance: like all fragile materials their resistance increases when their transversal size reduces.
Fibers in cluster can be produced directly or through the cutting of continuous filaments.
We can get them as wadding (wool), mat and felt.
Continuous fibers are carried out with a process of spinning through melting, that can be used with fibers that come out from melting materials (glass, mineral fibers).
Carbon fibers and ceramic ones are made from organic fibers, and these precursors are thermically degraded.
Precursors are prepared with the same technologies used to prepare conventional organic fibers.
When used as a reinforcement, yarn with 3000-12000 fibers is used (it is shortly called 3-12 K).
For some fibers we need CVD (Chemical Vapor Deposition) and a substrate of highly melting fibers: SIC or B4C on borate, TIN, SIC on carbon.
Inorganic Fibers |
Abbreviation |
CARBON |
(CF) |
GLASS |
(GF) |
METAL |
(MTF) |
BORON |
(BF) |
SILICA |
(SiC) |
SILICA CARBIDE |
(SiC) |
CERAMIC |
(CER) |
Kind of Fiber |
density (g/cm3) |
Tenacity (MPa) |
Modulus GPa |
|
Min |
Max |
Min |
Max |
Min |
Max |
Glass |
2,5 |
2,62 |
3400 |
4500 |
70 |
70 |
Carbon |
1,76 |
2,1 |
2000 |
7000 |
240 |
700 |
SiC |
2,55 |
3,5 |
2000 |
3700 |
200 |
420 |
Oxides |
3,9 |
3,9 |
1200 |
1400 |
340 |
400 |
|
Static Load
|
Dynamic Load
|
Thermic resoistance |
Density |
|
Tenacity
|
Modulus
|
Impact |
Fatigue |
|
|
|
Tensile |
Flexural |
Compressive |
Tensile |
Flexural |
Compressive |
|
|
|
|
Glass |
+ |
= |
+ |
- |
- |
- |
+ |
- |
= |
- |
Aramidic |
= |
- |
- |
= |
= |
= |
= |
= |
- |
+ |
Carbon |
+ |
+ |
= |
+ |
+ |
+ |
- |
+ |
+ |
= |
|
Glass |
Aramidic |
Carbon |
Density (g/cm3) |
2,5 |
1,45 |
1,8 (2,1) |
Tenacity (MPa) |
2000-4000 |
3000 |
3000-5000 |
Modulus (GPa) |
50-80 |
70-130 |
200-500 |
Elongation (%) |
4+5 |
2+4 |
|
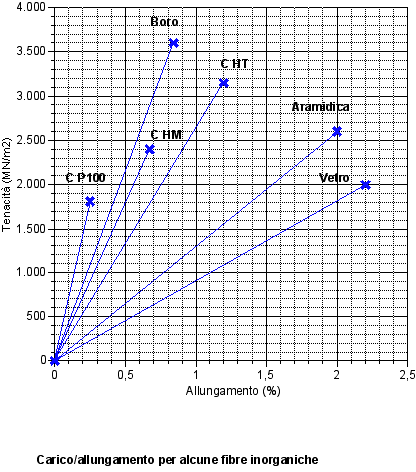
Stress/Strain of some inorganic fibers
Textile glass fibers (CF)
Glass fibers are mostly used as reinforcement of composite materials, whose performances, together with the low cost of fiber, make up for their negative sides, such as, for instance, the high weight.
The use of this kind of fibers in more proper textile areas, such as fittings, in order to exploit its good fireproof, is still limited.
Chemical composition and properties
Properties of glass fibers are bound to the chemical composition of the mixture, but they are also influenced by the spinning way.
Usually, they are divided into:
Use |
Type of Glass
|
Multipurpose fibers |
glass E,
|
Acid resistant fibers |
glass A, C, CR,
|
Alkali resistant fibers |
glass R, S
|
High strength fibers |
glass R, S
|
Fibers with good dieletric properties |
glass D.
|
Components
|
Standard
|
Acid resistance
|
Alkali resistance
|
Mechanical Resistance.
|
Electric applications
|
|
|
A
|
C
|
E-CR
|
|
R
|
S
|
D
|
Quartz
|
Si02
|
53-55
|
70-72
|
60-65
|
58
|
60
|
60
|
60-65
|
73-74
|
100
|
Al2O3
|
14-15,5
|
0-2,5
|
2-6
|
12-13
|
0,7
|
|
20-25
|
|
|
CaO
|
20-25
|
5-9
|
14
|
21
|
5
|
|
|
0,5-0,6
|
|
MgO
|
|
|
1-3
|
4,5
|
|
|
10
|
|
|
B2O3
|
|
|
2-7
|
<0,1
|
|
|
0-1,2
|
22-23
|
|
F
|
0-0,7
|
|
|
<0,15
|
|
|
|
|
|
Na2O
|
|
12-15
|
8-10
|
0,6
|
14
|
|
|
|
|
ZrO2
|
|
|
|
|
18
|
|
|
|
|
Main glass fibers producers
Trademark |
Firm |
Country |
|
BAYER AG FIBERGLAS |
D |
* |
FUIJI FIBER GLASS CO |
J |
* |
NIPPON ELECTRIC |
J |
* |
NIPPON GLASSFIBER |
J |
* |
NITTO BOSEKI |
J |
* |
SKANDINAVIAN GLASSFIBER |
S |
* |
VETROTEX |
F |
* |
VITROFIL |
I |
ARATON |
OWENS-CORNING CORP. |
I |
ASSEMBLOFIL |
NUOVA ITALTESS |
I |
BETA |
OWENS-CORNING CORP. |
I |
bi-ply |
OWENS-CORNING CORP. |
I |
CAM ELYAF |
CAM ELYAF GLASS FIBER |
TR |
chop-pak |
JOHNS MANVILLE CORP. |
USA |
CHOPVANTAGE |
PPG INDUSTRIES |
USA |
CONFORMAT |
NICOFIBERS |
USA |
CREEL-PAK |
OWENS-CORNING CORP. |
USA |
D-GLASS |
NUOVA ITALTESS |
I |
DELTACHOP |
PPG INDUSTRIES |
USA |
DURA GLASS |
JOHNS MANVILLE CORP. |
USA |
E-GLASS |
NUOVA ITALTESS |
I |
EVANITE |
EVANITE FIBERS |
USA |
FIBERGLAS |
FIBERGLASS CANADA |
CA |
FIBERGLAS |
OCTIGRAS |
BR |
FIBERGLAS |
OWENS-CORNING CORP. |
B |
FIBERGLAS |
OWENS-CORNING CORP. |
USA |
FIBERGLAS E |
OWENS-CORNING CORP. |
F |
FIBERGLAS VETROTEX |
GEVETEX-TEXTUILGLAS |
D |
FIBREGLASS |
FIBREGLASS P0LC |
UK |
G-GLASS |
NUOVA ITALTESS |
I |
GLASSLON |
ASAHI FIBER GLASS |
J |
IVEBERG |
NITTO SPINNING CO |
J |
MAXICHOP |
PPG INDUSTRIES |
USA |
MICROLITH |
SCHULLER INTERNATIONAL |
UK, USA |
MIRAFLEX |
OWENS-CORNING CORP. |
USA |
POLSILON |
CHEMITEX-ANILANA |
PL |
Q-FIBER |
SCHULLER INTERNATIONAL |
UK, USA |
QUARTZEL |
VETROTEX DEUTSCHLAND |
D |
R-GLASS |
VETROTEX ITALIA NUOVA ITALTESS |
I |
S-GLASS |
NUOVA ITALTESS |
I |
S-GLASS |
OWENS-CORNING CORP. |
I |
SILENKA |
SILENKA |
NL |
SILIONE |
VETROTEX DEUTSCHLAND |
D |
SURMAT |
NICOFIBERS |
USA |
TERMO-GLAS |
HKO |
D |
TEXOVER |
VIDRERIA ARGENTINA |
AR |
TUFROV |
PPG INDUSTRIES |
USA |
TURBOFIL |
VETROTEX FRANCE |
F |
TWINTEX |
VETROTEX |
F |
VETROTEX |
VETROTEX DEUTSCHLAND |
D |
VITROFIBRAS |
VITRO-FIBRAS |
ME |
VITRON |
SCHULLER INTERNATIONAL |
UK, USA |
Carbon fibers (CF)
Carbon fibers, that appeared on the market in 1960, are produced through alteration of organic fibers (rayon, acrylics etc) or from remainings of petroleum or tar distillation. The first ones are called Carbon-Pan, the others, Carbon from pitch (pitch).
Carbon fibers can be considered as a transition between inorganic fibers and organic fibers. The rigid structure of the strip cyclic links molecules or ladder ones of the carbon PAN or carbon-pitch fibers has suggested how to create aromatic organic molecules to get fibers with high performances.
Carbon fibers, discovered in 1879 by Edison, have been commercially produced only since 1960 following a process put right by William Watt for Royal Aircraft in UK. They represent the separation point between organic and inorganic fibers, being produced through modification of organic fibers or organic pitch.
Carbon fibers, together with glass fibers, have started the era of composite materials. Carbon fibers in particular have started the era of advanced composite materials, that were firstly used in the army and in aeronautics and later in automobile industry and in free time. Carbon fibers can be produced through heat treatment and pyrolysis of different polymeric precursors such as rayon, polyacrylonitrile, aromatic polyamide, phenolic resin etc. Recently carbon fibers and graphite fibers gotten from pitchy materials have been introduced. The words graphite fibers are improperly used, because these fibers dont come out from graphite, but from heat treatments over 2000°C of carbon fibers, when the carbon atoms place in a way similar to the graphite structure.
Carbon fibers from PAN
The precursor that has really started the era of carbon fibers (1960) is the polyacrilonitrile fiber, PAN, characterized by an adequate chemical composition, by a particular molecular orientation and by a specific morphology.
The chemical composition is important in order to moderate the exothermicity of the cycle reaction of CN, 18kcal/mass, heated to 220-260°C for some hours.
The result of the cycle reaction is a black colored, glow-proof material, oxidized PAN, that owns modest mechanical properties, and that is used for protective clothes, for glow-proof cotton-wool or in carbon-carbon composites, and for breaks requiring high performances (planes, race cars and high speed trains).
The following carbonization process (400-1000°C) is usually made in inert atmosphere or vacuum sealed and it removes atoms from the structure and it develops the graphitic structure.
From 400 to 1000°C, HCN, NH3 and N2 develop, also CO, CO2 and H2O can develop, according to the quantity of O2 that the oxidized precursor has bound when treated in air at a temperature of 220-260°C.
After the treatment at 1000°C, a fiber contains more than 90% of carbon and about 5% of nitrogen.
It is very important to check the retraction of the fiber during the cycle phase at 220-260°C, because in this phase the alignment of the molecular segment along the fiber is fixed and the final elastic forms depends form this orientation. The molecular orientation given to the original acrylic fiber influences the toughness and the elastic form of the resulting fiber. An excessive orientation is negative because it brings surface and internal faults in the fiber.
Carbon-pitch fibers
Pitch, or tar residue, is the residue of the tar or petroleum distillation and it is made of thousands of aromatic hydrocarbons with a molecular weight from 200 to 800, which form a multi eutectic system with softening temperatures between 50 and 300°C, that are by far lower than the melting temperatures of pure aromatic components.
A mesophase is formed through a thermic treatment between 400 and 450°C. It is liquid crystals with a molecular order that is intermediate between that of crystals and of liquids.
The molecules of the mesophase are oriented along the fiber by the flowing gradient during the extrusion from a capillary.
The process of carbon fiber production through pitch mesophase is reduced to essentials as follows: the pitch or tar precursor is thermically treated over 350°C to be converted in mesophase containing both phases, the isotropic and anisotropic one. After extrusion, at about 380°C, the isotropic phase is made unmeltable by thermofixing in air at a temperature that is lower than the softening point at about 300°C.
Fiber is finally carbonized at 1000°C or it is treated at temperatures over 2000°C in order to produce graphite fibers with a highly elastic form. The main advantages of this process are that no filament tension is requested during the carbonizing and graphitizing phases and times of the individual phases are much shorter than those of the PAN process.
The structural analysis of the fiver shows that the carbon layers are parallel to the fiber axis.
In the following table the main properties of carbon fibers made from PAN and pitch are synthetized.
Characteristics |
Fibers from PAN |
Fibers from pitch |
Tenacity (Gpa) |
1,8-7,0
|
1,4-3,0
|
Modulus (Gpa) |
230-540
|
140-820
|
Elongation at Break (%) |
0,4-2,4
|
0,2-1,3
|
Density (g/cm3) |
1,75-1,95
|
2,0-2,2
|
Productive capacity
The productive capacity of carbon fibers is valuable in about 12000 yearly tons. Changes, even important ones, are under way. To restrict all in the last 10 years we must mention the stop of the BSM-BASF production in USA for 1350 tons a year and of Grafil for 320 tons a year.
In Europe Courtaulds stopped their production in 1990 for 350 tons a year. In spite of crisis times, the consumer course is definitely positive.
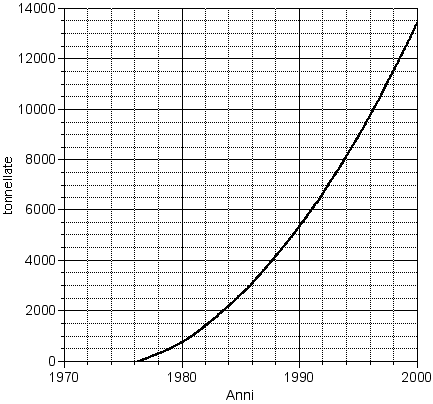
Fig. 1 Course of the world producing capacity
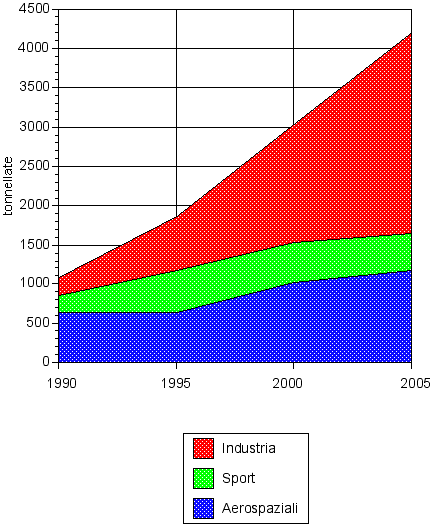
Fig. 2 evolution of the main markets (Europe)
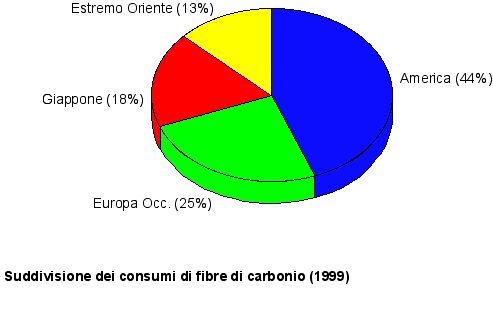
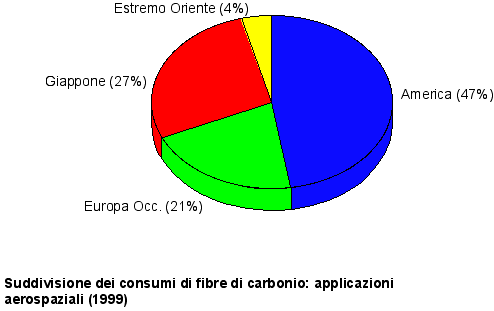
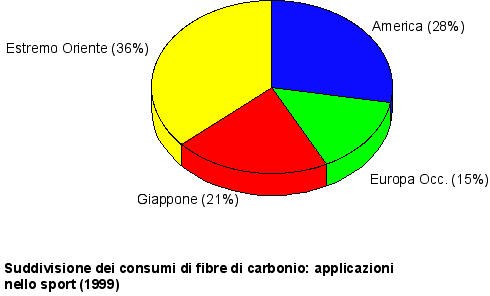
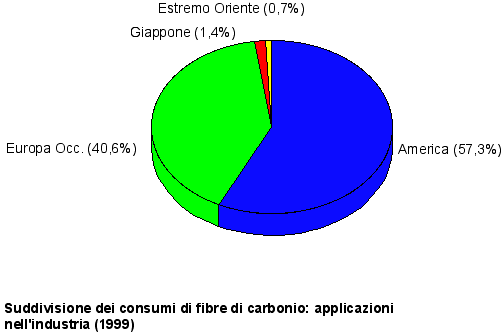
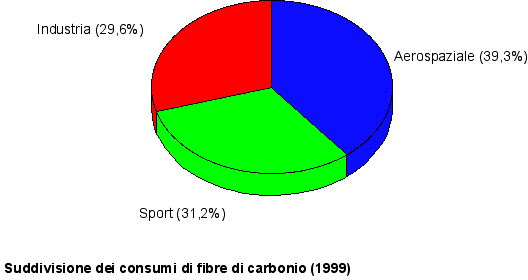
Main carbon fibers producers
Trademark |
Firm |
Country |
Web site |
|
FORMOSA PLASTICS CO. |
Taiwan |
|
BESFIGHT |
TOHO RAYON CO LTD |
J |
www.tohorayon.co.jp |
CARBOFLEX |
ASHLAND |
USA |
www.ashspec.com |
CELION (TOHO) |
BASF CORPORATION FIBER PRODUCTS |
USA |
www.basf.com |
CURLON |
RK CARBON FIBERS LTD |
UK |
|
DIALEAD |
MITSUBISHI RAYON |
J |
www.m-kagaku.co.jp/carbonfiber/index.htm |
FILKAR |
SOFICAR |
F |
|
FORTAFIL |
FORTAFIL FIBERS |
USA |
www.fortafil.com |
GRAFIL |
GRAFIL INC. |
USA |
www.grafil.com |
GRAFIL |
HYSOL |
UK+USA |
|
HI-CARBOLON |
ASAHI KASEI CARBON |
J |
|
KUREHA |
KUREHA CHEMICAL |
J |
|
LINEON |
RK CARBON FIBERS LTD |
UK |
|
MAGNAMITE |
HERCULES |
USA |
|
PANEX |
ZOLTEK |
USA,H |
www.zoltek.com |
PANOX |
RK CARBON FIBERS LTD |
UK |
|
PANOX |
SGL CARBON |
D, UK,F,USA |
www.sglcarbon.de |
PYROFIL |
GRAFIL INC. |
|
www.grafil.com |
PYROFIL |
MITSUBISHI RAYON |
J |
|
PYRON |
ZOLTEK |
USA,H |
www.zoltek.com |
SIGRAFIL |
SGL CARBON |
D, UK,F,USA |
www.sglcarbon.de |
SIGRATEX |
SGL CARBON |
D, UK,F,USA |
www.sglcarbon.de |
TENAX |
TENAX FIBERS (AKZO+tTOHO RAYON) |
D+J |
www.tenax.net
www.tenax-fibers.com |
THORNEL |
AMOCO FABRICS & FIBERS |
USA |
www.amoco.com |
THORNEL |
AMOCO FABRICS & FIBERS |
USA |
www.amoco.com |
TORAYCA |
SOFICAR |
F |
|
TORAYCA |
TORAY |
J |
www.toray.co.jp |
TORAYCA |
AMOCO FABRICS & FIBERS |
USA |
www.amoco.com |
The main world producer is TORAY, followed by TOHO RAYON.
SGL TECHNIK GmbH
They have over 6500 experts and a turnover of about 2,1 billions DM and they are the biggest world producers of carbon and graphite products.
They produce about 50% of oxidized PAN fibers that are commercialized with the trademark PANOX® and that are used for plane breaks, for insulation and for textile products.
SIGRAFIL C® carbonized fibers are used for electro-magnetic shielding, for anti-static spreading and to reinforce the composites.
We can have them both as filament and as clusters.
SIGRAFIL T® is a partially carbonized fiber (filament or cluster).
Different textile structures are set under the SIGRATEX® trademark, such as ribbons, woven, non woven, used as reinforcement for plastic materials and composites.
GRAFIL INC.
They are auxiliaries of Japanese Mitsubishi Rayon Co.LTD.
Carbon fibers produced here are used in aerospace (planes, helicopters, rockets, missiles, radars), in industry (infrastructures, medicine, oceanic platforms, cars, natural gas) and in sport (ski and skates, rackets, clubs and water sports). Fibers have GRAFIL® and PYROFIL® as trademarks.
TENAX Fibers GmbH & Co.
They were born from joint of AKZO NOBEL Faser (Germany) and Toho Rayon (Japan).
They produce about 1800 tons yearly, so they are the most important European producer.
The produced fibers are TENAX HTA, TENAX UTS and TENAX IMS.
MITSUBISHI CHEMICAL
This Japanese firm produces the DIALED carbon fiber.
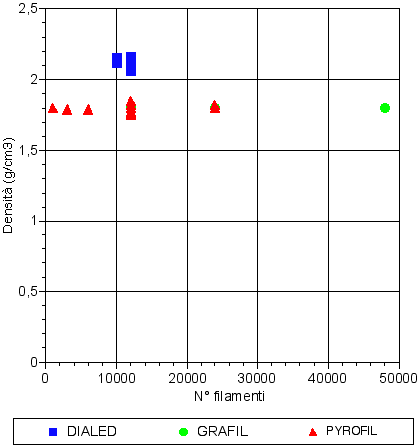
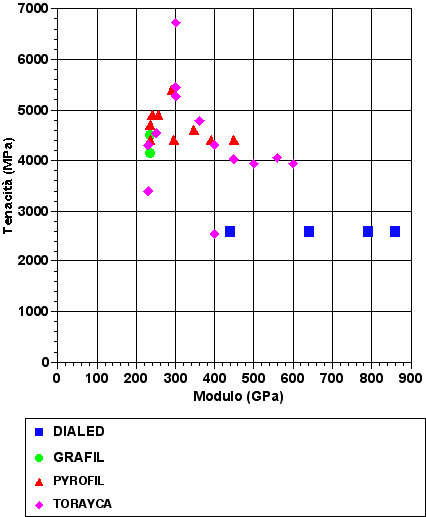
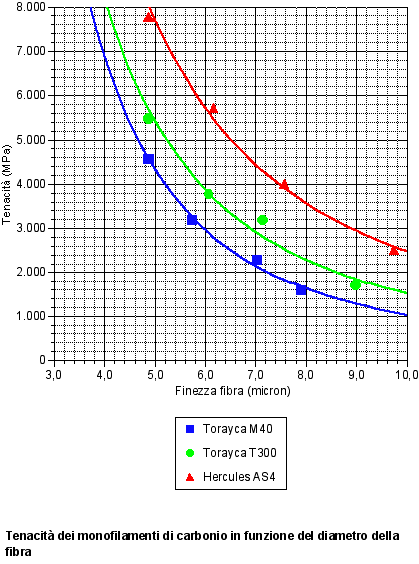
TORAY
The Japanese industry was the first one to sell a new kind of carbon fiber with 12000 filaments.
Their aim was to allow the production of fabrics for composites with a much higher covering factor than the one gotten with the previous kinds with 3000 and 6000 filaments.
This can happen because the yarn, thanks to an higher filament quantity, very much reduces the size of the spaces between the fibers in the fabrics, and as a result less resin is absorbed during the soaking.
Thanks to this new kind, fabrics (for composites) with about 200g/m2 weight can be made, the covering factor is very close to 100% and they are soft and easily to drape.
Furthermore, the so made composites are highly push resistant and have an high toughness. Nowadays ribbons with 48000 filaments are produced.
Toray produce carbon fiber TORAYCA®
SOFICAR
This French firm, owned by TORAY (70%) and by ELF ATOCHEM (30%), produces and commercializes European and Japanese made carbon fibers.
CERAMIC FIBERS
Ceramic fibers are mostly used as refractory fibers in uses over 1000°C and are characterized by a polycrystalline structure rather than amorphous.
Refractory ceramic fibers are mostly used for thermal insulation at high temperatures and to make special composites.
They are very expensive fibers because only a small quantity is produced, and they are used in particular fields such as aerospace.
Materials used are boron, silica, carbide, alumina, zirconia.
They show as filaments or very thin fibers (wiskers);bigger monofilaments or multifilaments can be used in textile transformation (yarn, ropes, parts of composites).
Their characteristics are bound to thin structure of the material, according to the kind of fiber.
Finally, there are more sophisticated kinds of fibers, with a basis of borate, carbide, silicon nitrure and borate nitrure.
Properties
Fibers act according to their shape and thickness.
The thinnest they are, the most flexible they are and they are used for light and soft refractories (the thicknest fibers give problems of skin irritation due to the penetration of these very thin fibers).
When fibers have a diameter over 1mm, they can be considered as transformable fibers according to the textile system.
Wiskers ar absolutely the most resistant (modulus>600Gpa, tenacity >20000 Mpa).
Chemical properties
Refractory fibers are low chemical reactive.
Their best characteristics are their oxidation resistance at high temperatures and their inactivity towards corrosion in composites with metal matrix.
Boron fibers suffer oxidation, so they are used with a surface cover gotten through vapor deposition.
Main ceramic and refractory fibers producers
Trademark |
Kind |
Firm |
Country |
ALMAX |
ALUMINA |
MITSUI MINING |
J |
BORON |
BORON, TUNGSTEN |
AVCO |
|
CERAFIBER |
ALUMINA SILCATE |
JOHNS MANVILLE CORP. |
USA |
FIBERMAX |
ALUMINA SILICATE |
CARBORUNDUM |
|
HAKOTHERM |
(SILICA) |
HKO |
D |
KAOWOOL |
ALUMINA SILICATE |
THERMAL CERAMICS |
|
KERLANE |
ALUMINA SILICATE |
KERLANE |
|
NEXTEL 312 |
BORATESILICONALUMINA |
3 M CERAMIC MATERIAL DEP. |
USA |
NEXTEL 440 |
BORATESILICONALUMINA |
3 M CERAMIC MATERIAL DEP. |
USA |
NEXTEL Z11 |
SILICA ZIRCONIA |
3 M CERAMIC MATERIAL DEP. |
USA |
NICALON |
SILICA CARBIDE |
NIPPON CARBON |
J |
SAFFIL |
ALUMINA |
ICI FIBRES |
UK |
SAFFIL HA |
ALUMINA |
ICI FIBRES |
UK |
SAFFIL RF |
ALUMINA |
ICI FIBRES |
UK |
SCS2 |
SILICA CARBIDE |
AVCO |
|
SICONEX |
SILICA ZIRCONIA |
3 M CERAMIC MATERIAL DEP. |
USA |
SILICATEX |
(SiO2) |
HKO |
D |
SILONTEX |
(CALCIUM SILICATE) |
HKO |
D |
TEXTRON BORON |
BO |
TEXTRON |
|
TEXTRON SCS |
SiC WITH CORE |
TEXTRON |
|
TYRANNO |
SiC WITH ORGANIC PRECURSOR |
UBE NITTO KASEI |
J |
ZIRLANE |
ALUMINIUM SILICATE |
KERLANE |
|
ZYBF-2 |
SILICA ZIRCONIA |
ZIRCAR PRODUCERS |
|
MITSUI MINING
Ceramic fibers NEXTEL® of 3M
NEXTEL fibers are continuous ceramic fibers and are an important model of refractory fibers. It is a continuous ceramic yarn, used to make products that have to suffer very high temperatures. Typical products are fabrics, ribbons, coverings, conveyer belts and insulating cables.
Their main characteristics:
Composition: 62% Al2O3, 24% SiO2, 14% B2O3
Working temperature 1200°C
Max temperature 1370° - 1800 °C
Nitric 50%
Hydrochloric 85%
Sulphuric 38%
Phosphoric <1%
Potassium <1%
Sodium <1%
Ammonia 78%
Calcium Hydrate 48%
Quantities are in percentage of the residual mechanic performances
The following table shows the main properties of NEXTEL yarns.
Composition (%)
Alluminium
Silica
Boron
Diameter (micron)
Title (den) 700
Density (g/cm3)
Tenacity (MPa)
Modulus (GPa)
Elongation (%)
Working temperature (°C)
Melting Point (°C) |
NEXTEL 312
62
24
14
10-12
600
2,724
1.725
138
1,2
1200
1.800 |
NEXTEL 440
70
28
2
10-12
700
3,045
2.070
186
1,1
1370
1.800 |
These fibers are usually gotten by melting a silicon and alluminium mixture and other chemical elements, such as zircon, chromium and thorium. They are mostly produced as clusters and, rarely, as filaments.
Their abrasion resistance is good: anyway, ceramic fibers distinguish themselves for their great resistance at temperature, that allows to continuously use them over 1000°C, until 2000°C, and for their high mechanic characteristics (toughness and form).
Thanks to that they can be used in specialized parts of:
-Gas filtering
-Electric, thermic and acoustic insulation
-Joints of gas pipes
- In composites reinforcements.
Boron fibers
BORON fiber is gotten through deposition of boron microgranules on a tungsten or carbonate yarn (diameter 12-17 micron).
Boron is a metal known for its exceptional resistance and form: even if it is very light as a filament, it has a triple resistance and a double form in comparison to steel. Among reinforcement fibers, borate is the only one that is exceptionally resistant to traction, compression and flexion, together with high form and low density
The physical-mechanical characteristics of BORON are:
- Density (g/cm3) 2,58
- Tenacity /CN/dtex)13,6
- Elongation at Break (%) 0,8
- Melting Point (°C) 2000
Besides the exceptional resistance to traction and temperature, boron fiber produced by AVCO shows good resistance to acids and alkali, to organic solvents, to ultra-violet rays and to micro organisms. It is a very particular fiber, gotten with sophisticated technologies and a complex production, so its cost is high. On the other hand BORON is almost only used in composites that suffer very high temperatures.
Metal fibers
Main metal fibers producers
Producer |
Country
|
AKZO NOBEL FIBERS B.V. |
NL
|
BEKAERT SA |
B
|
BRUNWICK CORP. |
USA
|
DORURES LOUIS MATHIEU |
F
|
NIPPON SEISEN |
J
|
ULTRA FIBRE |
USA
|
|