Circa la metà dei 45 milioni di tonnellate di fibre consumate annualmente sono fatte da polimeri sintetici.
Mentre la quantità di fibre chimiche cellulosiche vendute in Europa per i nontessuti si è mantenuta costante per 30 e più anni, il rayon viscosa quasi non ha partecipato alla massiccia crescita dell'industria dei nontessuti e oggi la sua quota di mercato è un decimo di quella del 1970.
Le fibre in fiocco di rayon viscosa erano, nel 1966, le fibre chimiche più a buon mercato. Oggi costano due volte le principali fibre sintetiche senza peraltro essere facilmente filabili o termocoesionabili.
In un momento in cui il premio per la biodegradabilità è praticamente inesistente queste fibre non possono costituire la materia prima per economici coverstock biodegradabili.
Dobbiamo allora analizzrae strade diverse per arrivare a nontessuti biodegradabili e lo faremo in due fasi. Cominceremo a vedere i recenti sviluppi nelle fibre sintetiche biodegradabili e poi torneremo a valutare nuove strade per nontessuti cellulosici che possano condurre alle maggiori riduzioni di costo.
Sintetici biodegradabili
La degradazione biologica delle fibre avviene quando si depolimerizzano i polimeri che le costituiscono in genere per l'azione di enzimi secreti da certi microrganismi. Questi enzimi idrolizzano o ossidano il polimero e possono agire sulle estremità della catena (esoenzimi) o in un qualsiasi punto della catena stessa (endoenzimi). Per far ciò l'enzima deve essere capace di legarsi alla fibra e di arrivare ai centri che possono essere idrolizzati o ossidati. Pertanto le fibre maggiormente biodegradabili sono quelle idrofile e formate da catene corte e flessibili con un basso livello di cristallizzazione.
Spesso hanno la catena principale con legami ossigeno o azoto e/o diramazioni laterali contenenti atomi di ossigeno o azoto. Questa descrizione corrisponde alla maggior parte delle fibre naturali e delle fibre formate da polimeri naturali. I polimeri non biodegradabili hanno caratteristiche opposte e ovviamente sono utilizzati per le fibre con maggior resistenza e durata. I polimeri senza ossigeno, come polipropilene e polietilene resistono completamente alla degradazione biologica.
Il poliestere aromatico (polietilentereftalato) nonostante contenga ossigeno resiste alla biodegradazione forse grazie alla catena rigida, simile ad una bacchetta. Lo stesso vale per le poliammidi nonostante contengano azoto.
Contrariamente agli aromatici, i poliesteri alifatici sono in genere biodegradabili. Si conoscono oltre cento specie di batteri in grado di sintetizzare e conservare poliesteri alifatici per utilizzarli in seguito come fonte di energia. Questi poliesteri oltre ad essere biodegradabili naturalmente, sono anche termoplastici e con essi, come con ogni altro poliestere, si possono formare film e fibre.
I poliesteri alifatici biodegradabili chimici sono ancora basati principalmente sulla polimerizzazione industriale di monomeri come acido glicolico (PGA), acido lattico (PLA), acido butirrico (PHB), acido valerico (PHV) e caprolattone (PCL).
Questi (Figura 1) e i loro copolimeri hanno anche trovato impiego nei trapianti, come suture riassorbibili, confezioni a rilascio controllato, film degradabili e stampi 1.

Fig. 1. Poliesteri alifatici biodegradabili
Grazie al grosso investimento annunciato quest'anno da Cargill Dow LLC, il tipo PLA sembra quello che potrà meglio rispondere ai requisiti per realizzare un coverstock biodegradabile a basso costo.
Fibre di acido polilattico
L'acido polilattico è stato realizzato per la prima volta da Carothers nel 1932, con un processo di condensazione e polimerizzazione diretta in solvente e sotto vuoto spinto dell'acido lattico. Abbandonò poi il polimero a causa del punto di fusione troppo basso per fibre e prodotti tessili e passò allo sviluppo del nylon.
Di recente il PLA è stato riproposto come legante alternativo per nontessuti cellulosici per la facilità di degradazione idrolitica rispetto all'acetato polivinilico o ai copolimeri dell'acido etilenacrilico.
Nontessuti spunlaid e meltblown sono stati studiati dall'Università di Knoxville nel Tennessee nel 1993 (3).
Kanebo (Giappone) ha introdotto nel 1994 la fibra Lactron® e nontessuti spunlaid per una capacità produttiva di 2000 tonnellate all'anno da espandere a 3000. Si è iniziato con applicazioni in agricoltura e nel 1998 c'è stato un rilancio per applicazioni nell'abbigliamento. Oggi la domanda giapponese di fibre PLA è di 500-1000 tonnellate all'anno. Si stanno sviluppano miste con rayon per ridurre i costi e migliorare la biodegradabilità.
Nel 1997 (4) Fiberweb (Francia) ha scoperto veli di nontessuto e accoppiati fatti in solo PLA e ha introdotto meltblown e spunlaid di PLA col marchio Deposa (5). Il polimero è stato sviluppato da Neste Oy.
I laboratori Galactic (Belgio) (6) hanno analizzato i polimeri dell'acido polilattico 6 concludendo che nel 2008 la produzione arriverà a 390.000 tonnellate e il prezzo sarà intorno a 2 dollari al chilo. Le loro stime di 70.000 tonnellate nel 2002 sembrano attendibili con il nuovo impianto di Cargill-Dow partito quest'anno. Resta da vedere se anche le previsioni di prezzo saranno giuste.
Cargill Dow Polymers LLC, oggi leader nella tecnologia dell'acido polilattico, è una joint venture 50-50 fra Cargill e Dow che risale al 1997. Attualmente hanno una capacità produttiva di 4000 tonnellate di polimero EcoPLA che raddopieranno entro l'anno per rispondere alle immediate richieste di mercato. A gennaio avevano annunciato la realizzazione di un impianto da 140.000 tonnellate all'anno per produrre il PLA NatureWorks, "una famiglia di polimeri completamente derivata da risorse rinnovabili annualmente a prezzi competitivi rispetto alle fibre e ai materiali per imballaggio tradizionali" (7). L'impiano partirà nel 2002 e molti produttori stanno già realizzando fibre dal nuovo polimero. (Fibre Innovation Technologies, Parkdale, Unifi, Interface, Woolmark, Unitika, Kanebo e Kuraray vengono menzionate come "alleati nello sviluppo").
Il loro processo (8) prevede l'estrazione di zuccheri (destrosio essenzialmente, ma anche glucosio e saccarosio) da farina di granturco, barbabietole da zucchero o amido di frumento e la successiva fermentazione ad acido lattico. Si preferisce partire da zuccheri raffinati piuttosto che dai meno costosi melassa o siero poiché la purificazione dopo fermentazione è più costosa.
L'acido lattico è convertito nel dimero (lattide) che è purificato e polimerizzato (metodo dell'apertura dell'anello) ad acido polilattico senza bisogno di solventi (Figura 2). La famiglia di polimeri nasce in parte dalla stereochimica dell'acido lattico e del suo dimero. Fermentato, l'acido lattico è per il 99,5% in forma L-isomero e per lo 0,5% in forma D-isomero.
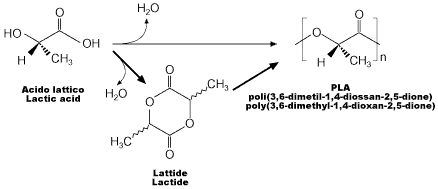
Fig. 2. Vie diretta e tramite dimero per il PLA 8
La conversione a dimero può essere controllata per avere tre forme differenti: L, D, e mesolattidi. (Fig. 3)
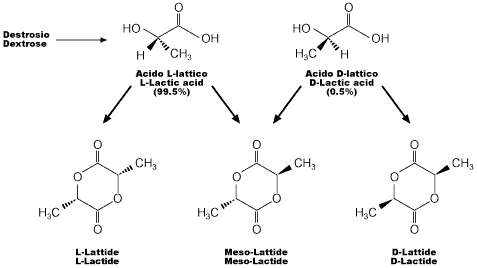
Fig. 3. Sono possibili tre diversi lattidi 8
La polimerizzazione del lattide verso polimeri ricchi di L-isomero dà prodotti cristallini, mentre quelli che contengono più del 15% di D-isomero sono più amorfi. Il miglior controllo della stereochimica che si realizza con la via del dimero spiega la superiorità dei prodotti attuali rispetto a quelli di Carothers del 1932. La resina PLA risultante può essere estrusa come le altre resine termoplastiche per formare fibre, film, spunbond, ecc.
Le fibre prodotte a partire dal già menzionato polimero EcoPLA si dice abbiano queste caratteristiche:
- In alcune forme ricordano PET o PS ed in altre PP e PE.
- Completamente biodegradabili in condizioni di compost.
- Convertibile in nontessuto con sistemi a secco, ad aria, ad umido, per filatura diretta, per deposizione.
- Capaci di conferire maggior resilienza, trasporto di umidità, traspirabilità e resistenza ad umido.
- Nel 1998 il prezzo era di 3-6 dollari al chilo, con riduzione fino a 1,1 dollari al chilo al massimo della produzione.
Recentemente si sono annunciati altri vantaggi per NatureWorks:
- Fibre a valore aggiunto basate su prodotti naturali.
- Colmano il fossato fra seta, lana, cotone e le fibre sintetiche.
- Mano e tocco superiori.
- Il comfort delle fibre naturali con le prestazioni delle sintetiche.
- Degradabilità controllata, capillarità migliorata, bassa pelosità.
- Eccellente recupero elastico e resistenza agli UV.
- Ridotta infiammabilità con poco fumo e scarsa generazione di calore.
Le applicazioni nei nontessuti riguardano: fibre per imbottiture, copertura di coltivazioni, geotessili, panni per asciugare, prodotti igienici e medicali, pannolini, fibre leganti.
Ovviamente il PLA può essere prodotto con differenti proprietà se non altro perché l'acido lattico, essendo chirale e con due centri di asimmetria, esiste in quattro differenti forme. Ha anche le proprietà richieste dai pannolini biodegradabili, essendo facilmente convertibile in film, fibra, spunbond e meltblown con le attuali apparecchiature di estrusione. Comunque il nuovo impianto da 140.000 tonnellate di polimero costerà 300 milioni di dollari e rimane da vedere se si potrà produrre o no a prezzi inferiori ai 50 centesimi di dollaro per libbra (che è il costo della resina PP e PET) che ne garantirebbero il successo.
Operano molti altri produttori. All'Index 99 NKK (Giappone) ha presentato un nontessuto spunbond da 15 grammi a metro quadrato con formazione e proprietà apparentemente eccellenti. Anche Kuraray (sempre Giappone) ha mostrato fibre PLA e ha fornito dati sulle sue proprietà e sulla velocità di biodegradazione. Polimero PLA è prodotto in Giappone da Mitsui Toatsu (col marchio Lacea per polimerizzazione diretta dell'acido lattico dal monomero), Toyobo, Dai-Nippon Ink Chemicals, Showa Polymers e Shimadzu Corp.
Proprietà delle fibre biodegradabili
La Tabella qui sotto riporta un confronto fra i dati pubblicati di cui disponiamo.
Proprietà |
CDP PLA |
Kuraray PLA |
Rayon |
Lyocell |
Poliestere |
Densità (g/cm3) |
1.25 |
1.27 |
1.51 |
1.52 |
1.38 |
Punto di Fusione (°C) |
120-170 |
170 |
None |
None |
260 |
Titolo (dtex) |
1.7 (e.g.) |
1.7 |
1.7 |
1.7 |
1.7 |
Tenacità (cN/tex) |
50 |
25-45 |
20-25 |
40-45 |
35-65 |
Allungamento (%) |
35 |
N/A |
18-22 |
14-16 |
15-40 |
Ripresa di Umidità (%) |
0.4 - 0.6 |
0.48 |
13 |
12 |
0.4 |
Sulla base delle informazioni disponibili il PLA sembra una fibra eccellente con le giuste credenziali tecniche per sostituire il polipropilene nei nontessuti. Come notato da Carothers, il punto di fusione appare tutt'ora troppo basso per scalzare la supremazia del poliestere aromatico nei prodotti tessili tradizionali.
Altri sintetici biodegradabili
Biopol di Monsanto ( originariamente sviluppato da ICI-Zeneca (9), con un impianto da 10.000 tonnellate all' anno nel 1987 ) era basato su un copolimero di 3-idrossibutirrato e 3-idrossivalerato ottenuti per fermentazione batterica.
Era venduto a circa 15 dollari al chilo per prodotti speciali e si pensava di averlo come fibra ad un prezzo molto più basso. All'Index 99 Monsanto ha annunciato di aver cessato il progetto nel gennaio 1999. Comunque la loro rassegna stampa (10) di ottobre 1999 segnala che la produzione diretta di PHBV e altri poliidrossicomposti, è una alternativa percorribile rispetto ai costosi processi di fermentazione.
Il policaprolattone è stato usato in mista con altre plastiche per realizzare film biodegradabili fin dagli ultimi anni '70. Unitika e Nippon Unicar svilupparono un nontessuto interlacciato ad acqua con 80% di cellulosa e 20% di fibre PCL (11). Freudenberg (Germania) sviluppò spunbond biodegradabili basati su PCL (50%) e "polimeri convenzionali per fibre" (50%) per indumenti di fatica, prodotti per l'incontinenza e prodotti per il bendaggio (12).
Bak di Bayer, una poliesterammide è basato su esametilediammina, butandiolo e acido adipico. Il butandiolo è anche la base di Bionolle, sintetico biodegradabile di Showa Polymer.
Eastar Bio di Eastman è un copoliestere basato su acido tereftalico e glicole etilenico.
Biomax di Dupont è basato su tre loro poliesteri alifatici e costo solo un po' più del PET convenzionale.
Procter e Gamble ha descritto (13) un processo che usa un polimero tipo Biopol (o altri sintetici biodegradabili) sia fuso che sciolto in solvente e filato in un nontessuto di microfibre da solo o insieme ad una varietà di fibre naturali. Un brevetto di quest'anno (14) si riferisce ad un polimero biodegradabile per lo strato superiore ed inferiore dei pannolini.
Cellulosici Spunlaid
Tutte le indicazioni suggeriscono che la biodegradabilità diventerà un punto importante di marketing se potrà essere conferita ad un pannolino senza sacrificare nessuno degli attributi delle marche più affermate. Nontessuti biodegradabili utilizzabili come coverstock esistono già in molte forme e una delle migliori è il rayon interlacciato ad acqua, ma nessuna può competere in termini di prezzo col polipropilene spunlaid o drylaid termocoesionato.
Inoltre per avere le stesse prestazioni del PP in termini di rewet il rayon interlacciato ad acqua avrebbe bisogno di un ulteriore finissaggio.
Se consideriamo il costo del nontessuto cellulosico al convertitore, in teoria il maggior guadagno si può ottenere passando dalle fibre in fiocco drylaid ad un processo spunlaid collocato nella fabbrica di cellulosa. Molto lavoro è già stato fatto in questo campo, la maggior parte prima che argomenti come la biodegradabilità e l'impiego di risorse rinnovabili raggiungessero la coscienza pubblica.
Le strade della viscosa cupro
Molti produttori di fibre di cellulosa hanno tentato di migliorare il rapporto prestazioni/costo producendo da sé i nontessuti.
- Courtaulds (ora Acordis), Rhone-Poulenc e Enka Glanstoff (ora Acordis) hanno sviluppato nontessuti spunlaid di rayon su scala pilota negli ultimi anni '60 e primi anni '70. Courtaulds ha rilanciato un prodotto basato su un nuovo processo nel 1978 ritirandolo nel 1982.
- Kanebo e Daiwabo hanno fatto ricerche su tecniche simili.
- Asahi ha lavorato con linee pilota di viscosa e cuproammonio prima di commercializzare la via cupro col marchio di nontessuti Bemliese®.
- Mitsubishi Rayon ha sviluppato un processo (poi venduto a Futamura) basato sullo xantato di idrossimetilcellulosa in cui i veli erano coesionati per punti in una calandra termica prima della rigenerazione.
- Kosabura Miura filava la viscosa in verticale con filiere oscillanti su un trasportatore e spruzzava i filamenti liquidi con acido.
- L'istituto di ricerca Tachikawa ha sviluppato un processo spunlaid per viscosa polinosica.
Asahi con Bemliese® e Futamura con TCF, producono entrambe coverstock ma su scala relativamente piccola e a prezzi scontati. Infatti è impossibili persuadere i fabbricanti di pannolini che questi smunlaid cellulosici possano essere un concorrente reale per un coverstock biodegradabile.
Forse il concetto dei Super-Impianti (preformatura dell'anima del pannolino mediante deposizione ad aria con una macchina da 100.000 tonnellate all'anno presso l'impianto della cellulosa (15) potrebbe ridurre drasticamente i costi di uno spunlaid di viscosa? Comunque il processo alla viscosa sta per essere superato da altri sistemi più ecologici per arrivare alle fibre cellulosiche ed è di questi che vogliamo parlare.
Fra le numerose vie possibili per arrivare alle fibre cellulosiche analizzate negli ultimi trent'anni, almeno quattro meritano attenzione per il nostro discorso. Tutte sono state sviluppate prima di tutto per i tessili tradizionali e si sarebbero potute evolvere in modo diverso se il mercato dei coverstock fosse stato un punto di riferimento attraente. Tutte appaiono più facilmente integrabili nella produzione della cellulosa di quanto non lo sia il processo alla viscosa.
La via del carbammato
Turunen (16) e Struszczyk (17) facendo reagire la cellulosa con urea ottennero una pasta stabile che poteva essere conservata indefinitamente e che si scioglieva facilmente in soda caustica. La soluzione risultante era anche facilmente filabile in acido o alcale diluiti formano fibre di carbammato di cellulosa o cellulosa rigenerata (o una miscela delle due).
Dal nostro punto di vista le fibre di carbammato di cellulosa appaiono più interessanti:
- Fibre col 2% di azoto resistevano alla biodegradazione senza per questo essere tossiche per gli organismi. Avevano anche una maggior assorbenza verso l'acqua ed erano solubili in soda caustica all'8%. Erano autoleganti nel processo di formatura del nontessuto ad umido.
- Le fibre diventano più biodegradabili ed insolubili in alcali man mano che si riduce il tenore di azoto (e la cellulosa rigenerata).
Il processo è stato realizzato su scala pilota da Saeteri (Finlandia) e si sono valutate piccole quantità di fibra in nontessuti, ma non spunbond, almeno a quanto risulta all'autore.
Pensando in termini di Super-Impianti l'impianto di cellulosa dovrebbe fornire non solo la pasta per l'anima del pannolino realizzata per deposizione ad aria, ma anche la pasta al carbammato per la fabbricazione del coverstock da realizzare sul posto via spunlaid per avere un economico recupero e riciclo dei vari prodotti chimici. Lo spunbond base potrebbe essere lavorato per realizzare topsheet, backsheet e l'acquisition layer.
Nel mondo più conservatore delle fibre tessili le proprietà del carbammato erano meno desiderabili di quelle del prossimo processo che prendiamo in esame: solubilizzazione e rigenerazione della cellulosa da soluzioni di ossido amminico.
La strada Lyocell
Il processo Lyocell impiega n-metilmorfolina-n-ossido per solubilizzare la cellulosa prima di filare la soluzione in acqua ed è stato sviluppato ed industrializzato per applicazioni tessili da Enka e Courtaulds (ora insieme in Acordis) negli ultimi 20 anni.
Offre un sistema accettabile per convertire la cellulosa naturale in un rayon di alta qualità completamente biodegradabile con caratteristiche meccaniche vicine a quelle del poliestere.
Inoltre questa tecnologia ha il potenziale per convertire la pasta in fibra a costi seriamente competitivi nei confronti di cotone e poliestere.
Visti i notevoli investimenti iniziali si è fatto per questa fibra (nel 1990) uno speciale lancio nel settore della moda. Il lancio ha avuto un grande successo e ha portato ad una rapida espansione dei consumi fino alla massima capacità produttiva che è di 100.000 tonnellate.
Comunque questo rappresenta solo una metà dell'uno percento del mercato attuale delle fibre cellulosiche e la fibra Lyocell è commercialmente ottenibile solo da due fonti, Acordis e Lenzing. Alceru (Schwarza), FCFC (Taiwan), Hanil Synthetic Fibre Co. (Corea) e Birla (India) stanno tutte lavorando su impianti pilota di Lyocell. Solo Lenzing sembra aver avuto anche la capacità teaorica di integrare il Lyocell con la produzione della pasta ed ha scelto di non farlo.
Il Lyocell fa nontessuti eccellenti, specialmente in quei processi che possono valorizzarne la superiorità estetica come l'agugliatura e l'interlacciatura ad acqua (spunlacing). La sua alta resistenza ha un valore intrinseco modesto per gli usa e getta, ma consente al produttore di ridurre la grammatura a parità di prestazioni. L'assenza di ritiro e l'elevata stabilità ad umido consentono rese elevate nei processi di interlacciatura ad acqua e l'elevato modulo evita il collassamento ad umido come per il rayon viscosa. La fibrillazione, cioè la formazione di microfibre sulla superficie ottenuta per abrasione ad umido o mediante getti d'acqua ad alta pressione, aggiunge nuove possibilità per lo sviluppatore di nontessuti. Sfortunatamente il suo posizionamento in una sfera di eccellenza ne ha finora impedito l'impiego nelle principali applicazioni usa e getta mentre si è affermato in alcune nicchie ad alto profitto.
All'industria dei nontessuti piace molto l'economicità del polipropilene dovuta al fatto che è un sottoprodotto dell'industria energetica. Il rayon viscosa richiede la solubilizzazione della pasta di cellulosa, un prodotto pregiato dell'industria del legno. Il Lyocell è oggi nelle stesse condizioni, ma la semplicità del processo produttivo ha il potenziale, finora inesplorato, di utilizzare paste a basso costo e quindi può ottenere economie di scala che possono risultare interessanti per i produttori di pannolini.
La possibilità di ottenere il Lyocell da paste a basso costo e di filarlo è descritta in un recente brevetto di Weyerhauser (18). Una pasta ricca di emicellulosa e con poca lignina è solubilizzata in NMMO per poi essere convertita in nontessuti via spunlaid, melt blowing o per filatura centrifuga.
Usando ancora una volta il concetto del Super-Impianto si può immaginare:
- Impianto Lyocell da 350.000 tonnellate (cioè delle stesse dimensioni di un impianto poliestere) collegato ad una fonte di pasta a basso costo per realizzare una fibra in sostituzione della viscosa, ai prezzi del fiocco di poliestere e per un'ampia varietà di applicazioni.
- Una grossa linea di nontessuto spunlaid che utilizzi la fibra di cui sopra potrebbe realizzare un'ampia gamma di nontessuti biodegradabili, compresi coverstock, backsheet e acquisition layer.
- Questi veli potrebbero essere coesionati in vari modi compresa l'interlacciatura ad acqua in linea.
- La tecnologia oggi usata per fare le fibre superassorbenti di Lyocell carbossimetilato, potrebbe essere usata per realizzare superassorbenti cellulosici spunlaid sul posto.
Solubilizzazione diretta della cellulosa in soda
Si sa da molti anni che la pastalegno si scioglie parzialmente in soda caustica diluita molto fredda e ci sono stati molti tentativi di migliorare questa soluzione fino al punto in cui sia possibile filare la miscela in fibre tessili. Kamide ed altri ricercatori, lavorando al Fundamental (Fibre) Research Laboratory di Asahi hanno descritto (19) le fibre filate dalla soluzione di cellulosa in soda caustica. Il passo fondamentale era l'"esplosione" mediante vapore della pastalegno per aumentare l'accessibilità alla catena cellulosica prima di venire in contatto con la soda caustica.
Struszczyk ed altri (20) hanno usato enzimi della cellulasi per modificare la struttura della cellulosa e consentirne la solubilizzazione in soda.
Questi metodi alla soda producono fibre con caratteristiche inferiori al rayon viscosa, che comunque sono più che adeguate, in termini di resistenza, per spunlaid e melt blowing.
Ancora una volta una vecchia tecnologia unita al concetto del Super-Impianto potrebbe diventare la base di un processo per nontessuti biodegradabili a basso costo.
Dissoluzione in acido fosforico
La cellulosa si scioglie in acido fosforico all'85% senza degradare e può essere rigenerata per filatura in acqua di fibre ad alto modulo. Però la concentrazione dell'acido fosforico diluito per il riutilizzo nella fase di dissoluzione è troppo costosa perché il processo complessivo risulti economico. Interessanti una recente serie di brevetti di Akzo-Nobel, uno a proposito della filatura per centrigazione di stuoie fibrose (21), un altro per produrre fibre superassorbenti di cellulosa in gel in forma ibrida (22).
Sintesi diretta di fibrille di cellulosa
Da menzionare il fatto che i batteri, in questo caso Acetobacter Aceti, producono fini fibrille di cellulosa quando siano coltivati nelle giuste condizioni. Weyerhauser ha commercializzato Cellulon® fibrille basate su questa tecnologia poi venduta alla Monsanto. Le fibre hanno un diametro inferiore a 0,1 micron e sono difficili da lavorare anche nei sistemi ad umido.
Discussione e conclusioni
Le fibre termoplastiche e biodegradabili fatte dal PLA hanno il potenziale per portare la produzione e la commercializzazione di prodotti usa e getta biodegradabili un passo avanti. Fibre di questo tipo sono filabili normalmente in coverstock utilizzabili nei normali impianti per la fabbricazione di pannolini usa e getta. La possibilità di modificare le proprietà del PLA selezionando accuratamente la miscela di isomeri e il metodo di polimerizzazione sembra consentire la realizzazione di fibre da amorfe a cristalline (anche bicomponenti) con tutta una varietà di punti di fusione, velocità di biodegradazione e resistenza meccanica.
Naturalmente le fibre possono essere utilizzate in molte applicazioni e sarà interessante vedere quali priorità assegneranno i produttori.
Quando si spendono per un polimero cifre dell'ordine dei 300 milioni di dollari è evidente che all'inizio la pressione economica è tale da spingere verso le applicazioni di maggior valore. Nel caso del PLA comunque il punto di fusione è simile a quello del polipropilene piuttosto che del poliestere e la possibilità di sostituire quest'ultimo nei tessili tradizionali è limitata.
Nei nontessuti ha il vantaggio chiave, rispetto ai cellulosici, della facile conversione in fibra e nontessuti spunlaid insieme alla resilienza e alla voluminosità necessarie per una buona asciugatura superficiale nei coverstock. Sembra che possa competere riguardo al prezzo con gli attuali nontessuti cellulosici, ma per esserne sicuri si deve aspettare che sia in funzione, nel 2002, l'impianto da 140.000 tonnellate.
Come per i futuri nontessuti cellulosici gli annunci di quest'anno sull'espansione del PLA riducono la già minima probabilità di qualsiasi investimento nella loro produzione su larga scala sia con le tecnologie attuali o con le possibili tecnologie future legate al concetto del Super-Impianto.
Riferimenti
- 1 Dumican B L, "Bioabsorbable Materials", Medical Textiles and Biomedical Polymers Conference, Clemson SC USA, 1989
- 2 Bonsignore PV et al, "Polylactic acid degradable plastics, coatings and binders" TAPPI Nonwovens Conference, Marco Island, 1992.
- 3 Wadsworth L et al, "Melt processing of PLA resin into nonwovens", 3rd Annual TANDEC Conference, Knoxville, 1993.
- 4 US Patent 5,702,826, Ehret P et al, Dec 30th 1997, assigned to Fiberweb.
- 5 P Ehret, "Deposa Nonwovens: Deposable disposables" INSIGHT 96 San Antonio.
- 6 Bogaert and Coszach, "Polylactic Acids: New polymers for novel applications Speciality Polymers Session, Index99 Geneva.
- 7 The Dow Chemical Company, Press Release 11/1/2000.
- 8 Lunt J, Shafer, A, "Polylactic Acid Polymers from Corn: Potential Applications in the Textile Industry", Cargill Dow Polymers LLC, www.cdpoly.com.
- 9 "Biopol set to go commercial" Plastics and Rubber Weekly, 10 Jan 1987.
- 10 "Biopol: A Natural Plastic for a sustaninable environment" Monsanto Press Release 7th Oct 99
- 11 New Materials Japan - June 1997 pps 7-8.
- 12 "Biodegradable Spunlaid Fabrics" Medical Textiles - Sept 1996 pps 2-3.
- 13 USP 5,653,930 (Aug 5th 1997) Noda I., Lampe R, Satkowski M, assigned to Procter and Gamble.
- 14 USP 6,013,590 (Jan 11th 2000) Noda I., assigned to Procter and Gamble.
- 15 Skov Jensen H. The Super Site Concept - Really big airlaid machines for the prodution of baby diapers. Insight 99, San Diego.
- 16 "Fibres made by Wet Spinning of Cellulose Carbamate Solutions", Turenen et al, Neste Oy. TAPPI International Dissolving and Speciality Pulp Conference 1983.
- 17 Struszczyk H. Cellulose Carbamate and its utilisation. ACS, New Orleans, 1990.
- 18 Luo, Roscelli, Neogi, Sealy and Jewell "Lyocell fibres and compositions for making the same" WO 9947733 to Weyerhauser Sept 23rd 1999.
- 19 Kamide et al. "New Class of Cellulose Fibre spun from the novel solution of cellulose by wet-spinning method" J.App.Poly.Sci., 44,691-698 (1992).
- 20 Strusczcyk et al, "Celsol - Biotransformation of cellulose prior for fibre spinning" Cellucon 94, Bangor UK.
- 21 Westerlink, Maatman and Boerstoel, WO 97/28298 to Akzo Nobel, 7/8/97.
- 22 Westerlink, Maatman and Boerstoel, WO 97/30090 to Akzo Nobel, 21/8/97.